Liquid Sensors
The liquid sensors from AST often combine several measuring principles in one sensor. For example, the level measurement is often combined with a concentration/quality measurement of the liquid. The technologies used for level measurement range from ultrasound and capacitive systems to hydrostatic pressure measurement. The most suitable measuring principle is selected on the basis of customer requirements and the respective installation space situation.
In addition to ultrasonic systems, thermal conductivity measurements are often used to determine concentration/quality. In addition to high-precision density measurement, sensors based on the tuning fork principle also allow the viscosity of the respective medium to be measured. Measurements based on the resistive and capacitive measuring principle round off our product portfolio for liquids. Concentration measurement is used, for example, to determine the ethanol concentration of cleaning fluids in the wiper water tank (Clear Vision systems) and in exhaust gas aftertreatment with AdBlue® (measurement of the urea concentration). These technologies can also be transferred to other industrial segments, for example to determine the quality of various liquids, and can easily be expanded to include functions such as high-precision level measurement and the determination of electrical conductivity.
All AST sensors have a µController and are therefore able to calculate complex algorithms directly on the sensor. An output signal prepared in this way is made available in analogue or digital form.
Clear Vision Sensor
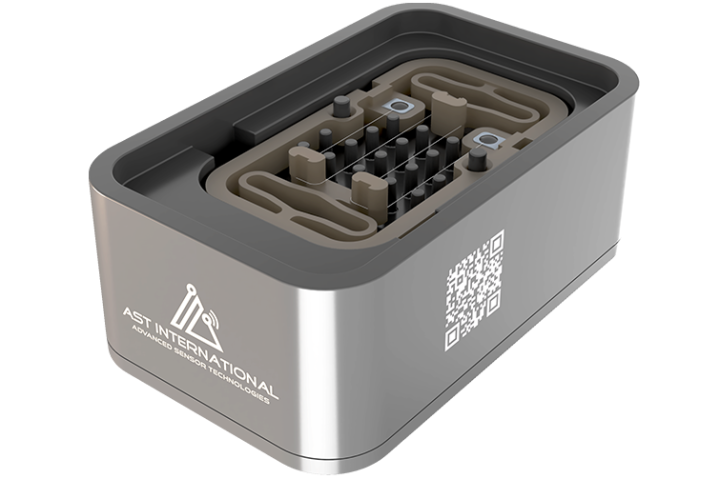
Regardless of whether a vehicle is already (partially) autonomous or manually operated, driving is only possible with perfect visibility for both the driver and optical assistance systems.
Especially in poor weather conditions, this can only be ensured if there is sufficient liquid of the right quality in the cleaning system.
AST sensors continuously measure the fill level, temperature, and concentration of ethanol in the cleaning liquid (cleaning effect/antifreeze). This allows the driver to refill in time and start his journey safely. Autonomous systems use our information to determine whether a smooth ride can be guaranteed via intelligent algorithms.
Battery Cooling Fluid Sensor
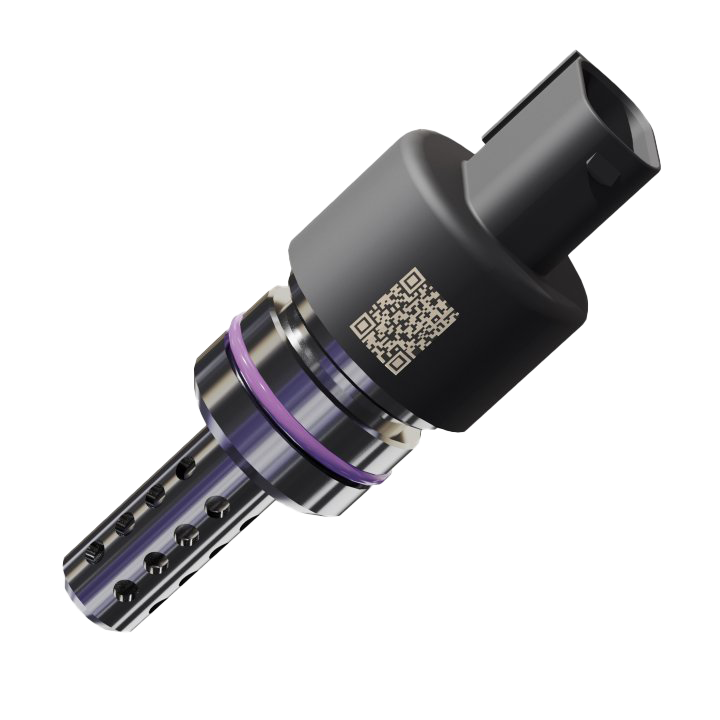
Monitoring the coolant used for the direct cooling of high-performance vehicle batteries is essential for the safe operation of such systems. Especially the isolation resistance of the cooling liquid is a very critical parameter, but monitoring other fluid parameters that change with aging will help determine the optimum time for maintenance. AST's BCF sensors determine not only the isolation resistance but also the relative dielectric constant. This means they can report back continuously on the condition of the coolant and pending service work for it.
AdBlue ® Sensors
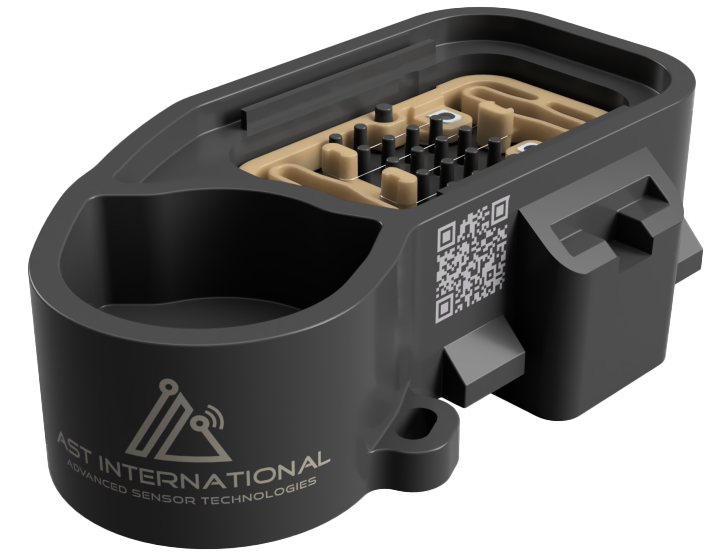
In diesel vehicles, exhaust gas treatment with AdBlue® reduces nitrogen oxide (NOx) emissions by up to 90 percent. Engines equipped with this technology require sufficient amounts of AdBlue® liquid in the required quality to run smoothly.
AST's sensors monitor the fill level in the AdBlue® tank so that drivers have plenty of time to refill their tanks. The sensors also measure the quality of AdBlue®, which consists of a mixture of urea (32.5%) and demineralized water.
This ensures compliance with legal requirements and prevents misuse.
Water Injection Sensor
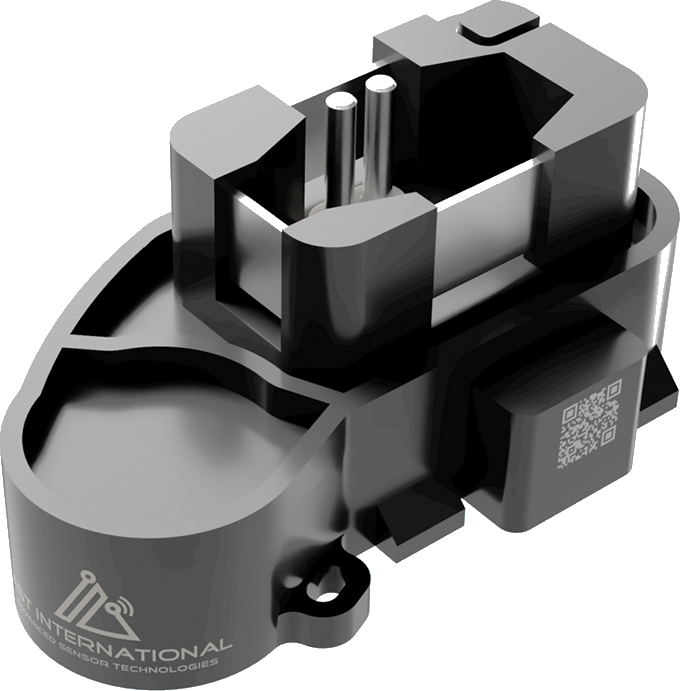
Water injection is a method of decreasing temperatures in internal combustion engines. It boosts performance while reducing fuel consumption and emissions.
To prevent damage to the engine, it is important to ensure that there is always sufficient demineralized water and no foreign liquids such as gasoline or windshield wiper fluid in the water tank.
AST's sensors detect foreign liquids by measuring conductivity, among other things, since distilled water is not conductive. Other non-conductive liquids can also be reliably detected.
Multi-measurement Sensors
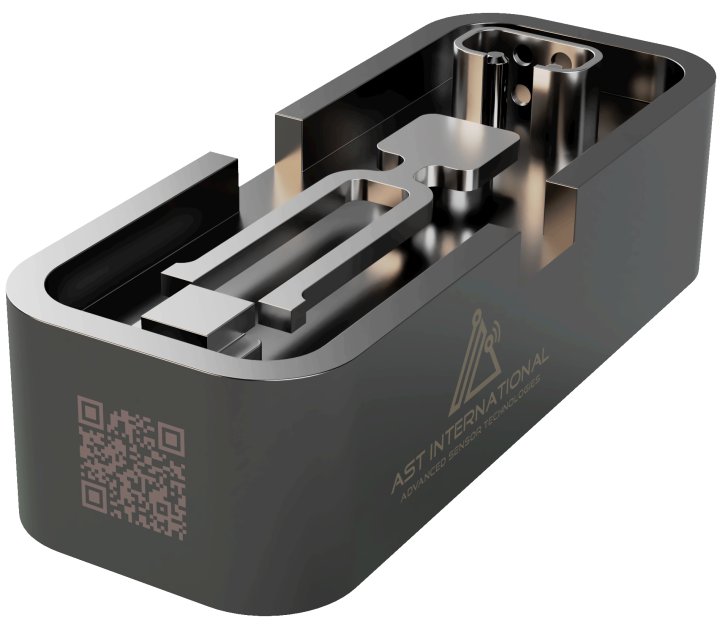
Besides preventing cost-intensive maintenance, monitoring the properties of liquids is an important task that enables the right actions to be undertaken based on the knowledge gained. The in-line detection of parameters providing information on component wear and the condition of fluids enables the optimum maintenance time to be defined and, as a safety function, the system to be shut down in the event of a detected malfunction, for example.
The AST Multi-Measurement Sensors determine a liquid's density and viscosity, isolation resistance, and relative dielectric constant. This multi-dimensional approach offers excellent performance in terms of accuracy and measurement result reliability.
Level Sensor
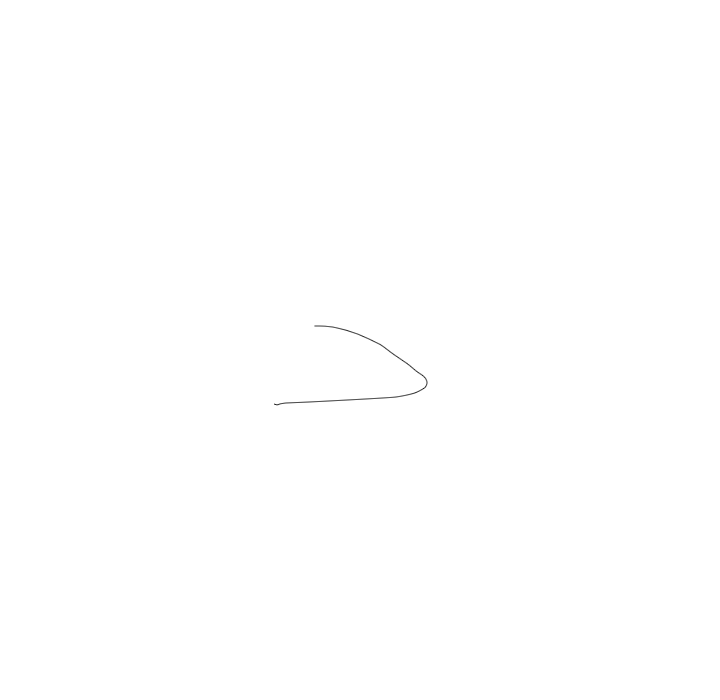
The level sensor is an indispensable instrument for monitoring and controlling liquids in various industries. With precise measurement using the capacitive measuring method, the level sensor is capable of providing accurate information about the quantity of liquid. Our technology eliminates the need for moving mechanical parts such as a float in the liquid container, ensuring high durability and enabling wear-free use even in demanding environmental conditions. The level sensor can be installed in containers of all types.