Position & Force Sensors
AST position sensors are designed to determine relative movements between two mechanical components and are adapted to the respective application. This entails using either 3D Hall or inductive technologies. The stationary part of the sensor interacts with the target attached to the moving part via a contactless and wear-resistant inductive or magnetic coupling. The shape of both the stationary sensor part and the target can mostly be adapted to the respective application. 3D Hall technology offers many advantages from being able to define positioning in up to 3 axes with measuring ranges of up to100mm whereas inductive technology demonstrates its strengths in one-dimensional measurements in ranges of up to 500mm. Both technologies feature sensors where both the stationary and the moving parts are protected by encapsulation against environmental influences, thus enabling their use even under adverse environmental conditions. Besides the “position", its derived quantities such as "velocity" or "acceleration" can also be recorded by the sensor. The position sensors are used in applications ranging from the measurement of brake pad wear in the mobility sector to applications for robot grippers and detecting imbalance, e.g., in industrial machinery.
AST's force/torque sensors utilize the strain on the given mechanical structure by the applied forces and torques. This strain is measured by the sensor using the differential eddy current principle, which achieves a resolution in the nanometer range. The existing structural component serves as a reference for the force-torque measurement whereas the shape of the sensors can mostly be adapted to the conditions of the structural mechanics. In most cases, a housing that seals off the structural component protects the sensor from environmental influences up to a protection class of IP6K9K. Our force/torque sensors are deployed, for example, in the electrically operated brakes of vehicles or for determining torques in motors and transmissions.
All AST sensors have a microcontroller and can calculate complex algorithms directly at the sensor. An output signal processed in this way is made available in analog or digital form.
Wear Sensor
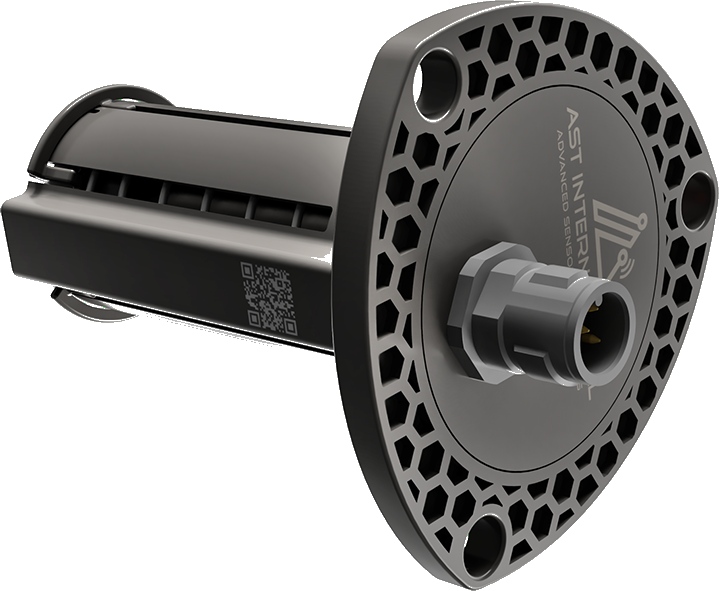
Every mechanical assembly is subject to a certain amount of wear the longer it is used. This becomes evident from, among other things, the change of a component’s shape or mechanical wear in the form of material erosion on the component’s surface. These mostly undesirable changes occur, for example, in clutches, transmissions, and brakes.
Wear impairs components’ function and effectiveness, which can lead to serious component damage and related failure. In practice, this entails the investment of additional time over and above the usual service intervals. What is merely an annoyance for the users of private vehicles leads to considerable downtime costs for commercial vehicles such as trucks or buses. After all, downtime is synonymous with lost earnings. Therefore, one tries to limit wear to easily replaceable components so-called wear parts.
Appropriate algorithms can be used to issue extremely accurate predictions about changes to the operating condition within the assembly since our intelligent sensors continuously monitor the wear on safety-relevant components and, on request, we can also determine the current temperature. This enables the individual optimization of service times. For example, our sensors in brake systems can determine whether a brake disc has been warped by thermal overload, or whether contamination is limiting the effectiveness of the brake piston, thus avoiding breakdowns and critical driving conditions.
Inductive Position Sensor
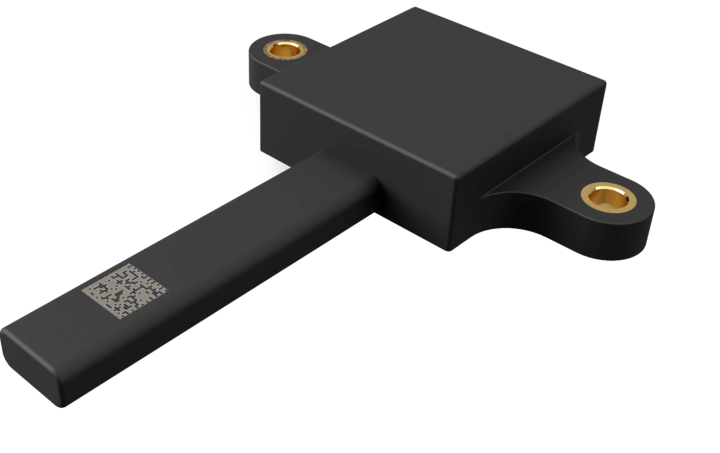
Based on the principle of inductive measurement, our position sensors determine the position of mechanical components in a contactless and wear resistant manner. The so-called target is attached to the moving part of the mechanical system and contactless interacts with the stationary sensor system via inductive mechanisms. The sensor and target are each encapsulated against environmental influences, enabling operation in harsh environments.
This enables, for example, the position of clutches, dampers, and hydraulic cylinders to be measured.
Unbalance Sensor
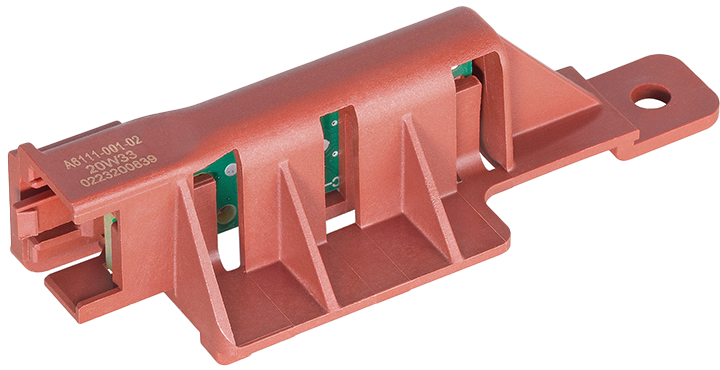
An imbalance can result from, for example, the rotating components in a machine being subjected to unfavorable loads. At high speeds, this imbalance causes increased wear and jeopardizes safe operation due to large forces. In such cases, an unbalanced sensor ensures that the device is not damaged.
Our sensors permanently monitor the load and movement of the rotating components in the device. The unit control evaluates the data, informs the operator about the status of the load, and adjusts the speed accordingly as necessary.
Force & Torque Sensor
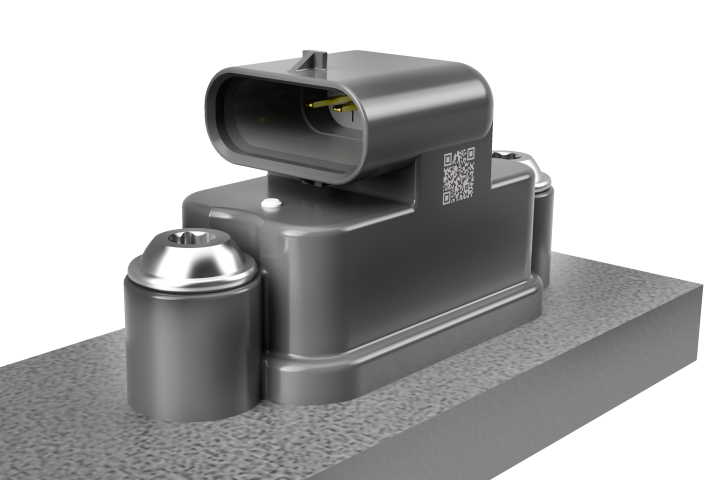
Ast´s inductive force and torque sensors enable the use of structural components for measuring forces and torques. The acting forces and torques lead to minimal structural deformations, which can be precisely detected by the sensitive sensors. The measurement principle is based on eddy currents and can detect changes in shape even down to the nanometer range. The sensor electronics can be integrated into the sensor element or connected via a cable. Especially in high-temperature environments, it is recommended to keep the electronics box separate.